To explain why PLC with CAN bus will become the mainstream
There must be one or more communication interfaces on the PLC for connecting to the corresponding communication bus. At the same time, the PLC will also have several IO interfaces, that is, data input and output interfaces. When working, the operator issues a start command to the PLC through the host computer. This command is transmitted through the communication bus we just mentioned. After the command reaches the PLC, it will pass a specific O according to the pre-programmed command. The interface is sent again. Why is the O interface not the I interface? You can actually understand by their names, the O interface is the OUTPUT interface, that is, the output interface. Correspondingly, the I interface is the INPUT interface, that is, the input interface. The data sent out through the PLC is naturally the output data, then it is very normal through the O interface. Then, the data reaches the designated machine through the line connected to the O interface, and the machine is started. The starting data may be a change in voltage, a change in current, or a change in temperature. It still depends on your original How to set it up. After the related machinery and equipment receive the instruction to start, it will generate a piece of data when doing work. It will flow back to the PLC through the I line, that is, the data input line, and then undergo corresponding processing (according to the previously compiled program). The communication bus finally returned to the upper computer, forming a round of operation. The PLC is a device that can continuously repeat the above operations according to the first programmed program.
We know that most of the PLCs now only have two types of communication interfaces: serial interface and Ethernet interface, but the CAN bus interface is obviously stronger than theirs, but it is missing. Compared with serial bus and Ethernet bus, CAN bus has faster data transmission speed, longer data transmission distance, more connectable node devices, stronger anti-interference ability, higher cost performance, can use CAN bus communication, which is still round Get the other two? But the reality is that there are very few PLCs with integrated CAN interface, so if the demanders want to achieve the above purpose, they have to connect a serial port to CAN or Ethernet to CAN gateway converter between the ordinary PLC and CAN bus. Of course it is a good way, but if you get a PLC that integrates the CAN bus directly, wouldn’t it be possible to avoid even those troubles? Therefore, in order to meet the needs of everyone, Shenyang Guangcheng Technology has launched the corresponding PLC device with CAN bus, which is the GCAN-PLC series.
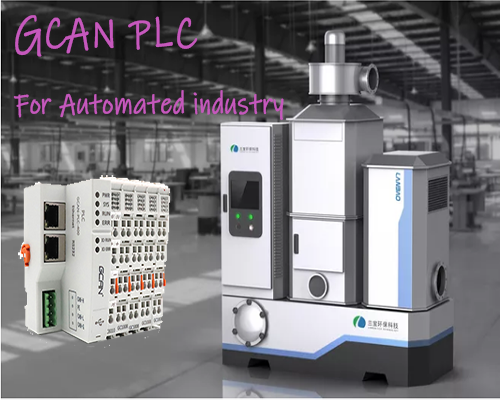
We know that most of the PLCs now only have two types of communication interfaces: serial interface and Ethernet interface, but the CAN bus interface is obviously stronger than theirs, but it is missing. Compared with serial bus and Ethernet bus, CAN bus has faster data transmission speed, longer data transmission distance, more connectable node devices, stronger anti-interference ability, higher cost performance, can use CAN bus communication, which is still round Get the other two? But the reality is that there are very few PLCs with integrated CAN interface, so if the demanders want to achieve the above purpose, they have to connect a serial port to CAN or Ethernet to CAN gateway converter between the ordinary PLC and CAN bus. Of course it is a good way, but if you get a PLC that integrates the CAN bus directly, wouldn’t it be possible to avoid even those troubles? Therefore, in order to meet the needs of everyone, Shenyang Guangcheng Technology has launched the corresponding PLC device with CAN bus, which is the GCAN-PLC series.
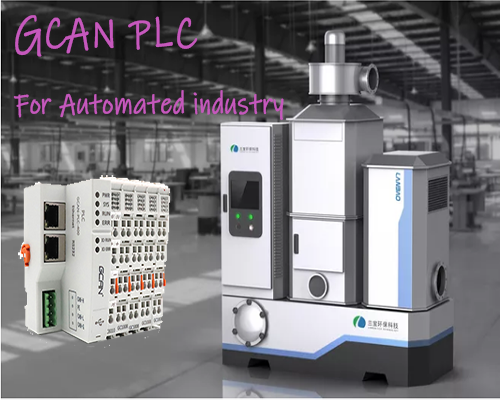
Shenyang Guangcheng Technology GCAN-PLC series PLC with CAN bus is a bus module controller with integrated PLC function. It has the characteristics of compact shape and high cost performance, and can be used to connect CAN bus system, Modbus system and distributed bus terminal modules, and these terminal modules can be expanded in a modular manner.
Shenyang Guangcheng Technology GCAN-PLC series PLC with can bus consists of a programmable main control module (GCAN-PLC-400), several GC series IO modules (GC-1008, GC-3804, etc.) and a terminal composition. The GCAN-PLC-400 main control module can be connected to all GC series IO modules. The user can choose to expand the IO module according to the actual needs of the site. The number of expansion IO modules can reach 32. The GCAN-PLC-400 main control module supports automatic configuration, users do not need to set parameters on the PC, the main control module will be automatically configured according to the front and rear positions of the inserted terminal module.
Shenyang Guangcheng Technology GCAN-PLC series PLC with can bus consists of a programmable main control module (GCAN-PLC-400), several GC series IO modules (GC-1008, GC-3804, etc.) and a terminal composition. The GCAN-PLC-400 main control module can be connected to all GC series IO modules. The user can choose to expand the IO module according to the actual needs of the site. The number of expansion IO modules can reach 32. The GCAN-PLC-400 main control module supports automatic configuration, users do not need to set parameters on the PC, the main control module will be automatically configured according to the front and rear positions of the inserted terminal module.