Obd product introduction
First of all, as a bus system mainly used in industry, the CAN bus must have certain anti-interference ability. If it is easily affected by external interference, how do you proceed with the next device operation? This also benefits from the voltage differential signaling mode of the CAN bus itself, which has been replaced by other buses and has long since failed due to interference problems.
Secondly, the data transmission distance of the CAN bus is relatively long, and the maximum distance can reach 10 kilometers. Of course, this is the farthest distance in theory. If it is the distance that can be applied to actual demand, it may be reduced a lot. But forty meters is absolutely guaranteed. In the 40-meter range, the CAN bus can maintain a baud rate of up to 1 Mbps, which is already outstanding in various industrial buses. If you are looking for another industrial bus that can beat the CAN bus data transmission speed, it can only be RS485. However, Lenovo's weak anti-jamming capability of the 485 bus, you will once again put the hug back to the CAN bus here.
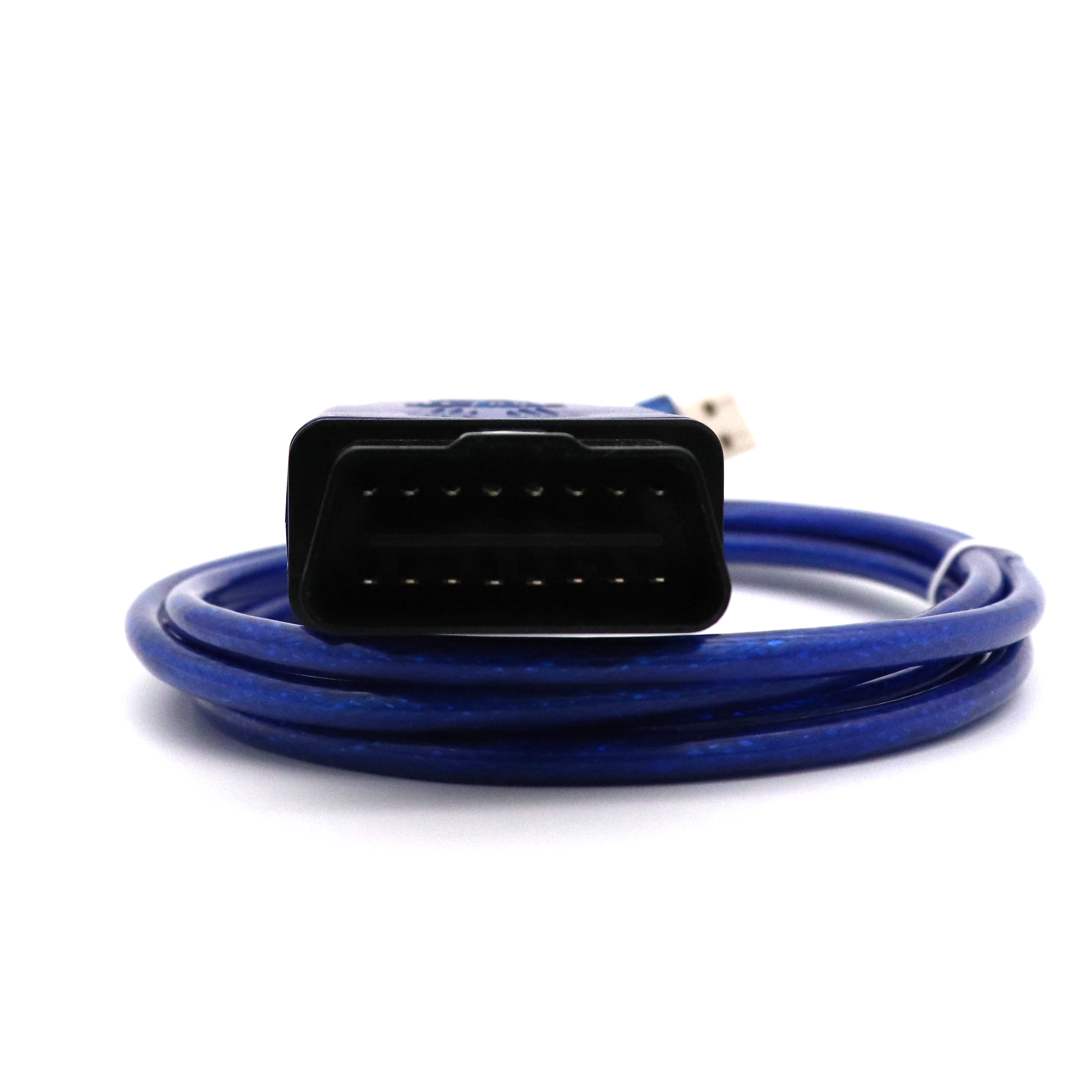
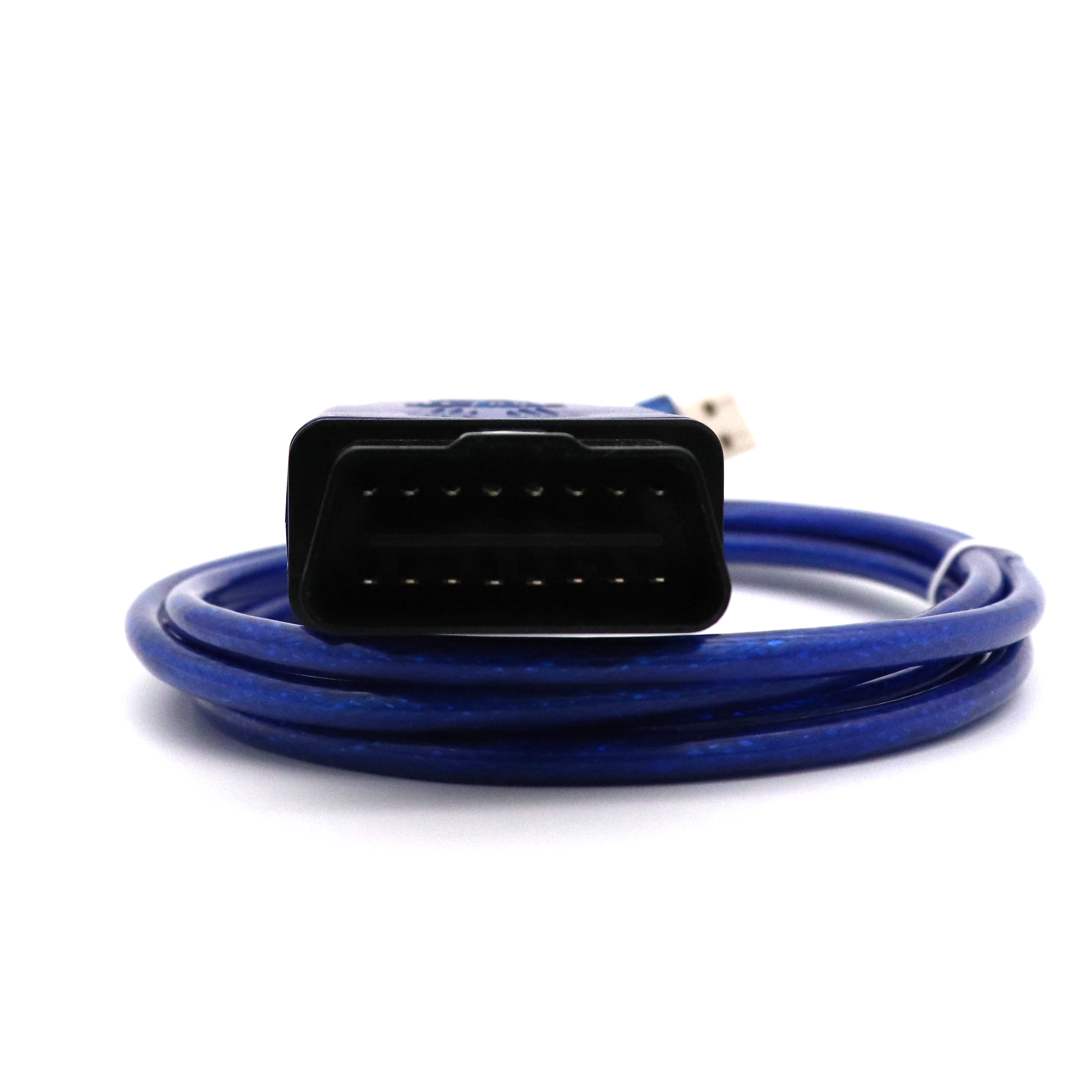
Third, the number of connected node devices of the CAN bus is relatively large. In theory, a CAN bus can connect 128 node devices at the same time. Of course, this is the most ideal condition. Generally speaking, it is ok to connect one hundred. But even then, it is more than enough to use on a device like a car. Even with larger vehicles with more node equipment, the two CAN buses can basically meet all control needs. It is specially developed for automotive control.
Luxury car using CAN bus as a communication control system
However, although the CAN bus has the above advantages, it is still a kind of artificial invention. It is not perfect. Just as we humans continue to work and fall ill, the car CAN bus will have symptoms of fatigue for a long time. Because it is controlled by the car, the result of the CAN bus problem is very terrible. Therefore, we need to guide the car CAN data through the OBD interface of the car for research. The specific tools required include: a computer capable of running CAN data detection software. Automotive OBD data analysis software like Guangcheng Technology ECANTOOL. A USBCAN OBD analyzer device that can connect to the computer's USB interface and connect to the car's CAN bus. Of course, you also need special guidance, the specific method of use can be learned through the manual. By connecting the above devices, we let the car's CAN bus data be transmitted to the CAN analyzer through its own OBD interface. The CAN analyzer converts this CAN data into USB data recognized by the computer and finally reaches the computer. The engineer judges whether there is a problem with the internal CAN bus of the car through the change of the CAN data displayed on the computer software, and performs the next operation according to the result, and completes the reading and detection analysis of the OBD data of the entire vehicle. In this series of processes, tools such as the Guangcheng Technology USB CAN OBD Automotive CAN Analyzer show a very prominent role.
Guangcheng Technology USB CAN OBD Automotive CAN Analyzer is a portable CAN-bus bus communication interface card with an integrated 1 channel CAN interface. This type of CAN card is designed by our company for automotive electronics development or automotive fault diagnosis. It uses USB CAN-OBD portable CAN interface card. The PC can be quickly connected to the CAN-bus network in the car OBD interface through the USB interface so that the PC can be constructed. CAN-bus network control node for data processing and data acquisition in the automotive CAN-bus network.
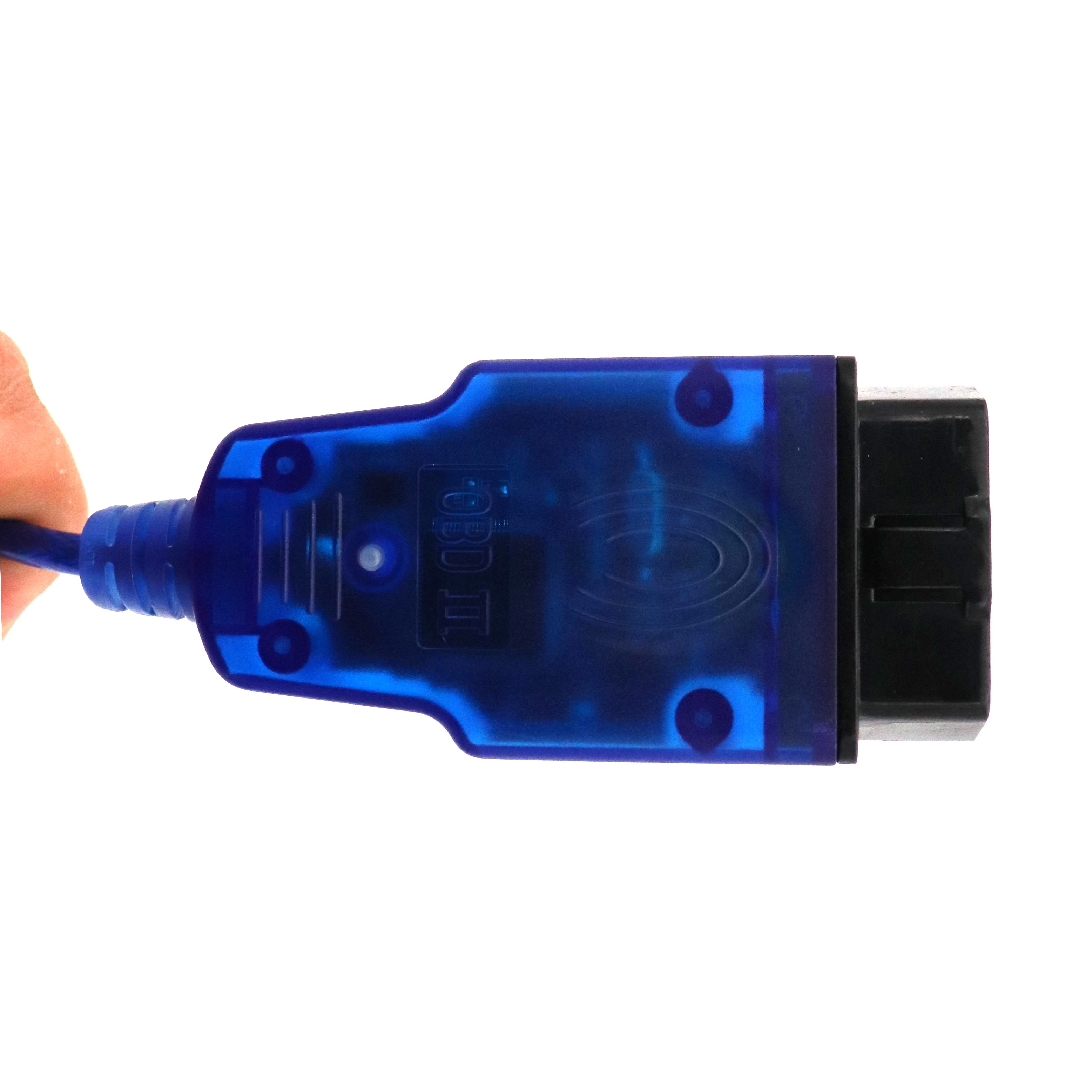
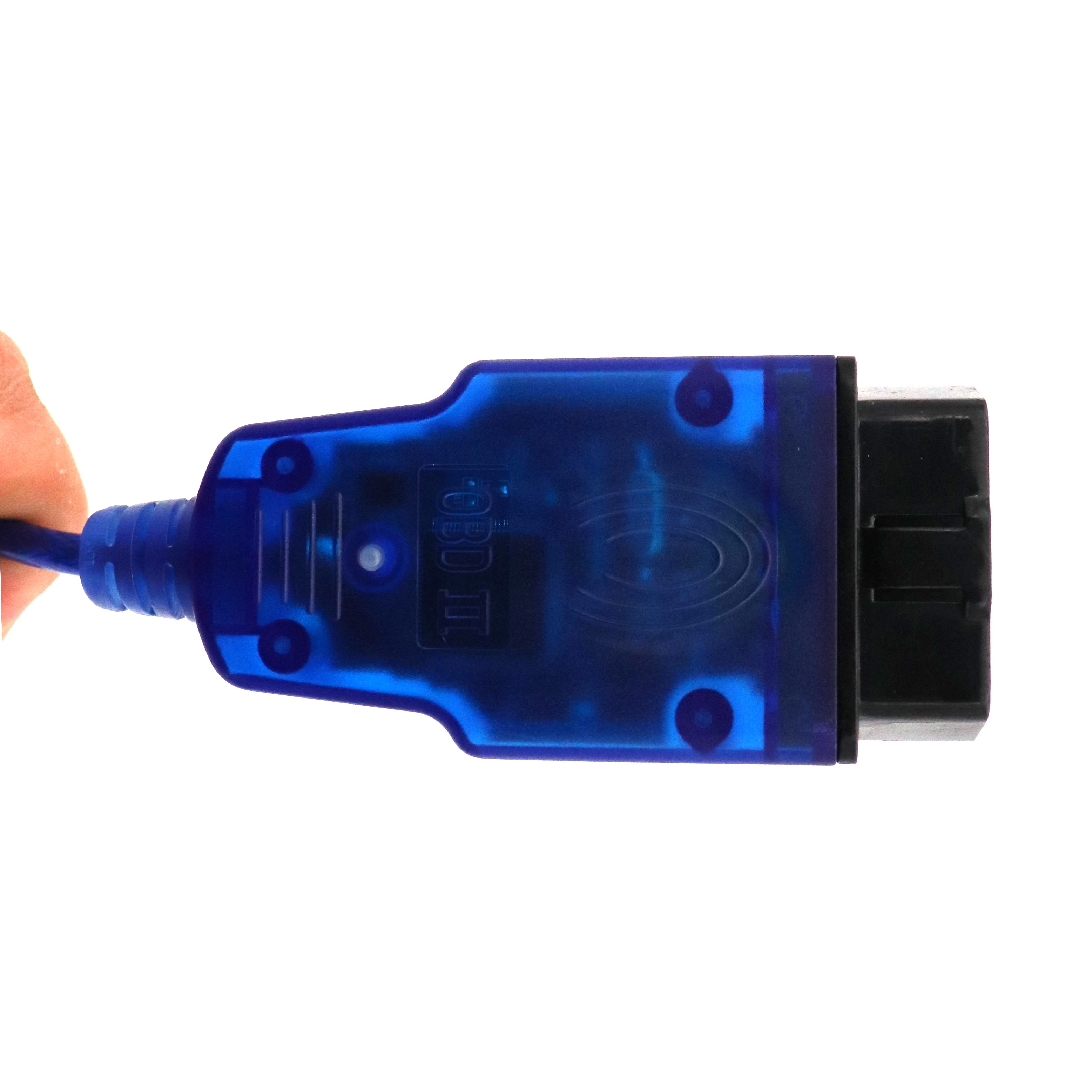