What are the main functions and applications of PLC?
PLC is a new generation of industrial control equipment based on automatic control technology, microcomputer technology, and communication technology. With the development of microprocessor technology, PLC has developed rapidly and has been trained in various fields of society. More and more applications. At present, PLC has been widely used in various industries such as steel, petroleum, chemical, electric power, building materials, machinery manufacturing, automobile, textile, transportation, environmental protection, culture, and entertainment.
As shown in Figure 1, the composition of the plc
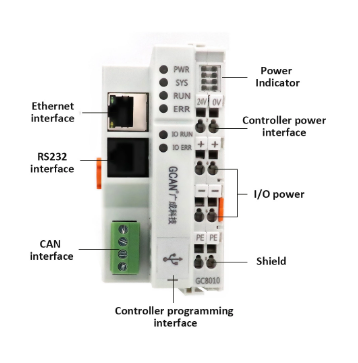
It replaces the traditional relay circuit and implements logic control and sequence control. It can be used to control individual equipment, multi-unit control, and automated assembly lines. Such as injection molding machines, printing machines, binding machines, combination machine tools, grinding machines, packaging production lines, electroplating lines, etc.
1, analog control In the industrial production process, there are many continuous changes, such as temperature, pressure, flow, liquid level, and speed are simulated. For the programmable controller to process the analog quantity, A/D conversion and d/A conversion between analog (analog) and digital (digital) must be implemented. PLC manufacturers produce matched A/D and d/A conversions. This module allows a programmable controller to be used for analog control.
2, motion control
The PLC can be used to control circular motion or linear motion. From the perspective of control mechanism configuration, early use of switching I / O modules to connect position sensors and actuators, now generally uses a dedicated motion control module. For example, a single-axis or multi-axis position control module that can drive a stepper motor or a servo motor. Almost all the major PLC manufacturers in the world have motion control functions, which are widely used in various machines, machine tools, robots, elevators, and other occasions.
4, process control
Process control refers to closed-loop control of analog quantities such as temperature, pressure, and flow. As an industrial control computer, the PLC can program various control algorithm programs to complete closed-loop control. PID regulation is a more common adjustment method in closed-loop control systems. Large and medium-sized PLCs have a PID module. Currently, many small PLCs also have this functional module. PID processing is usually a dedicated PID subroutine. Process control has a wide range of applications in metallurgy, chemistry, heat treatment, boiler control, and other applications.
5, data processing
Modern PLC has mathematical operations (including matrix operations, function operations, logical operations), data transmission, data conversion, sorting, table lookup, bit manipulation and other functions, which can complete data collection, analysis, and processing. These data can be compared to reference values stored in memory to perform certain control operations or can be communicated to other smart devices using communication functions, or they can be used in large scale control systems, such as unmanned control. Flexible manufacturing systems; also used in process control systems such as large control systems in the paper, metallurgical and food industries.
As shown in Figure
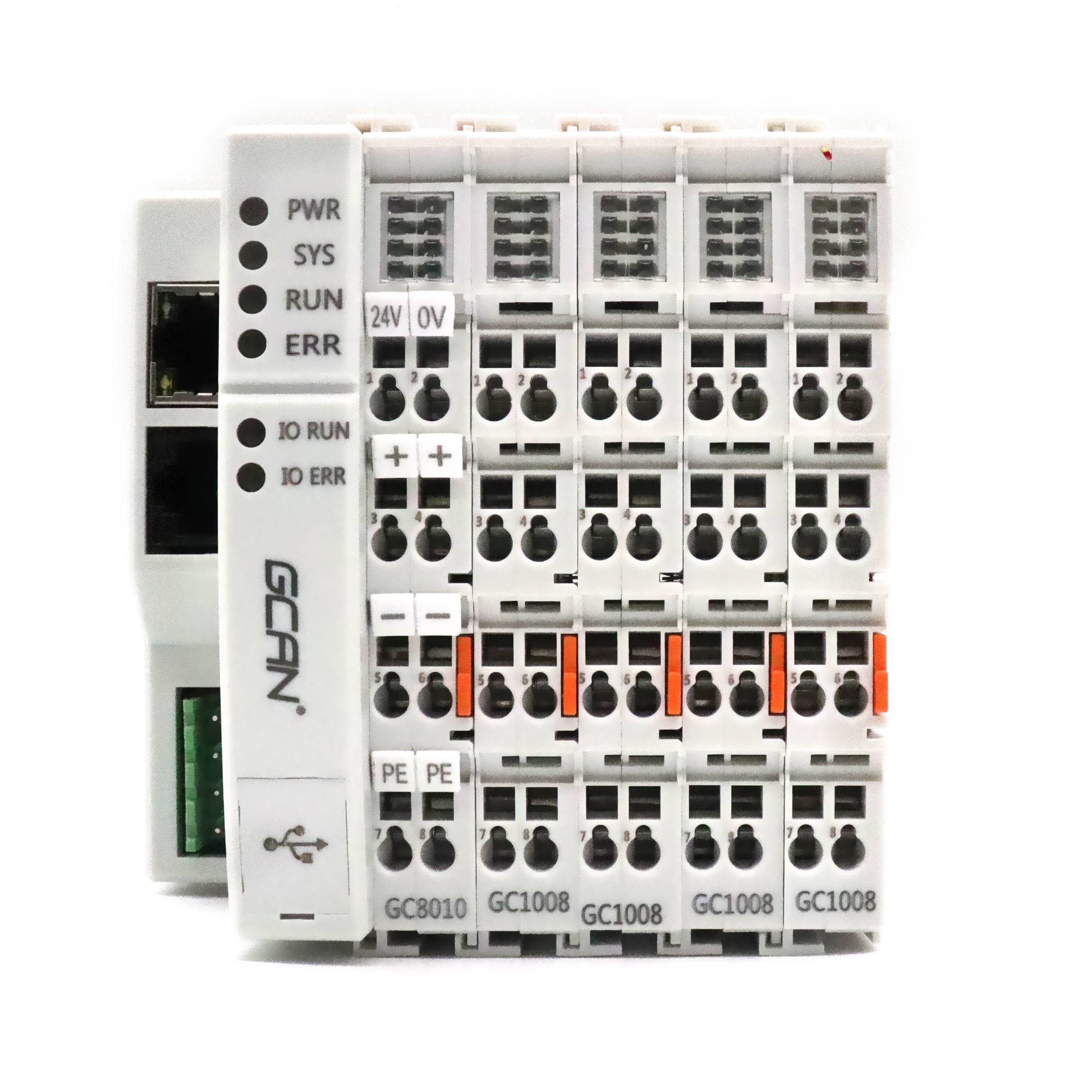
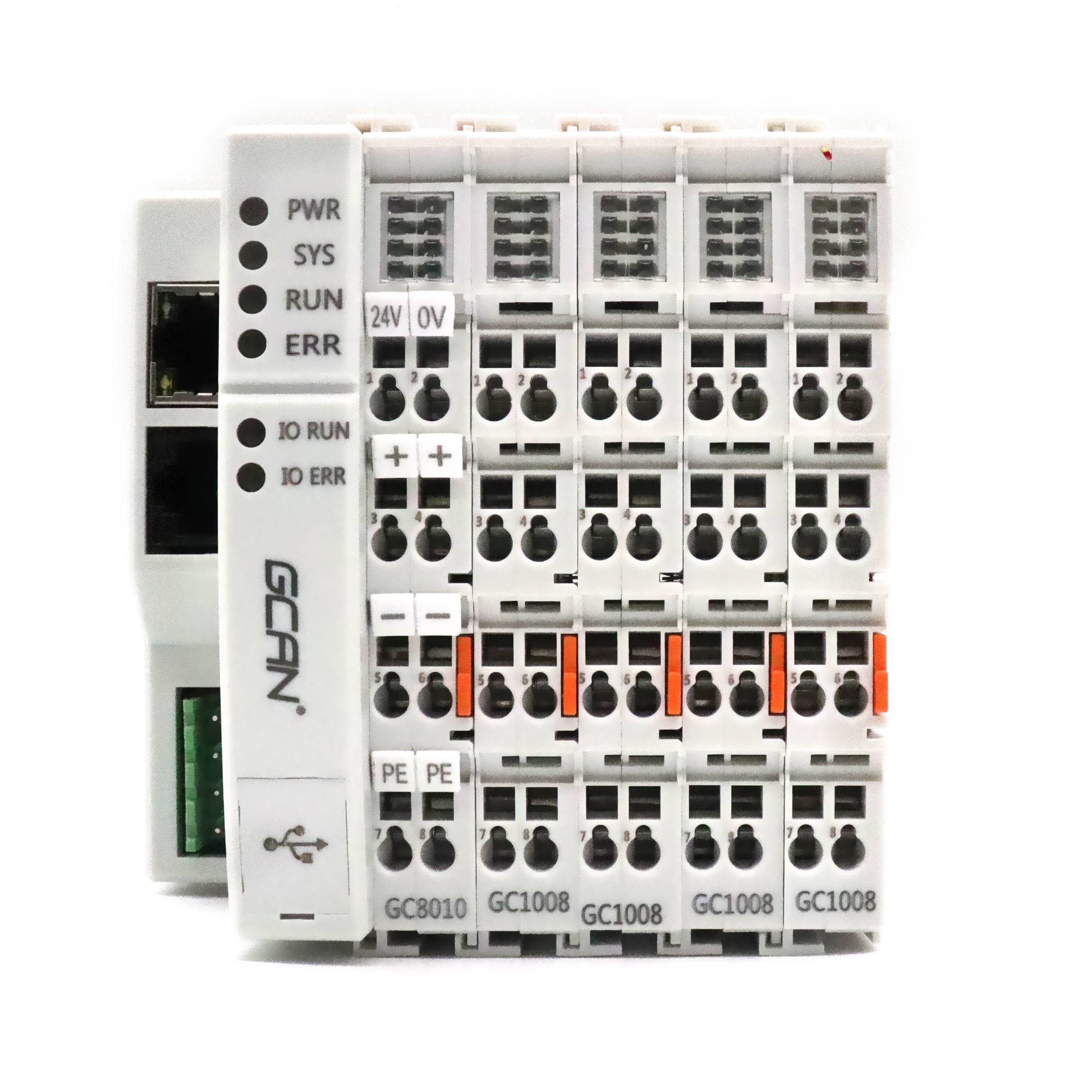
PLC communication includes communication between PLCs and communication between PLCs and other smart devices. With the development of computer control, the factory automation network has developed rapidly. Every PLC manufacturer attaches great importance to the communication function of PLC and has launched its network system. The newly produced PLCs all have communication interfaces and communication is very convenient.